What Factors Can Affect the Accuracy of Your Scale?
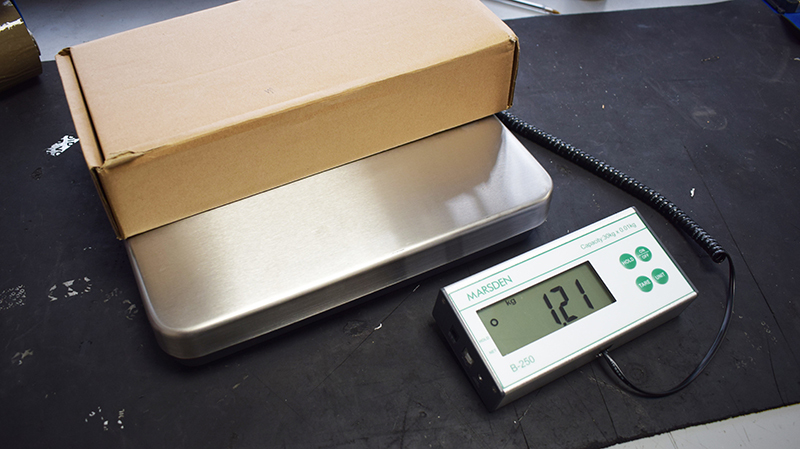
Pictured above: Marsden B-250 Bench and Floor Scale.
Marsden has been working in the weighing scale industry for over 90 years and we consider ourselves to be experts in this field.
We offer optional services for all of our customers. Our trained specialists can quickly spot any external factors that may be affecting the accuracy of a scale, including re-verifying faulty scales.
Unfortunately, even scales of the highest-quality can be affected by external factors. If you are worried your scale isn’t as accurate as usual, try considering the options below.
6 Factors that effect scale accuracy
1. Load Cell Accuracy
A scale would not be able to function without a load cell. A load cell is one of the key components in any digital weighing scale.
When an item is placed on a scale, the load cell will bend and it is this movement that is used to measure weight. If a load cell is not working then this can cause unreliable and inaccurate readings.
But what are the different factors that can affect a load cell? There’s 6 in total.
Response Time
The response time of a load cell is how long the load cell takes to stabilise and present an accurate reading. While this may not be an issue for most businesses, if you operate in a fast-moving checkweighing environment, for example, this could cause inaccurate loads.
Similarly, if you do not give your load cell enough time to return to zero then the scale will not be able to accurately give a result. This can cause errors with the weight reading. Allowing more time between each weighing can help to fix this.
Try doing multiple tests with your scale to work out its response time. This will help you to resolve both issues as you will then know the optimal time scale for each step.
Creep
If an item is left on a scale for a long period of time, this can cause creep to take effect. This can result in a change in the measured weight of an item if a load cell remains under pressure.
This is not an issue over a couple of minutes but for long periods of time, such as monitoring inventory, this can begin to occur.
Hysteresis
Hysteresis refers to the difference between two weight readings when the same load is measured. One reading is taken by increasing the weight from zero, while the second is obtained by decreasing from the cell’s maximum capacity.
Temperature Changes
If the temperature of the environment surrounding the weighing instrument fluctuates often, this can cause weighing errors. Sudden increases in temperature can cause load cells to expand or contract. Sometimes you can get load cells that are temperature compensated to reduce this effect, but even this is not guaranteed.
To prevent this from happening, you should consider using a space with stable temperatures. This issue is noticed particularly in weighing scales that are stored outdoors, as they’re exposed to hot, direct sunlight and then cold nights. You could try shielding your equipment from direct sunlight or choose portable scales that can be brought inside.
Non-linearity
Non-linearity can also cause errors. It’s the load cell calibration curve’s maximum deviation from a straight line, starting at zero load and ending at the cell’s maximum rated capacity.
Non-repeatability
If a load is repeatedly loaded under identical conditions, non-repeatability is the maximum difference between the repeated readings.
Gravitational Effect
Scales will react differently when used in different locations on Earth, as gravity is not the same everywhere. For most scales this is not an issue, but this change can be noticed in more precise laboratory balances. That’s why it’s important to get your balance calibrated when it’s moved often, even if this is just up a few flights of stairs.
2. Scale Load Factors
How you load the scale can also result in an inaccurate weight. There are a few tips to follow when properly loading or unloading a scale:
Ensure that the mounting structure located on the floor underneath the scale can fully support the weight of not just the scale, but its components and its load without flexing.
Check that the load is properly aligned, so that the load cells don’t interpret the force as weight and generate inaccurate readings.
It’s very important to ensure the mounting hardware is functioning properly as this is where the weight of the load placed on the load cell is channeled.
You can also use cross braces on scales that have less than ideal support legs to help reduce instances where support legs will spread under strain and lead to inaccurate readings.
If using a drive-thru scale, ensure that the drivers go slowly to prevent sudden changes.
3. Environmental Factors
Anything in the vicinity of the scale that can cause a negative effect on its weighing ability, is known as an environmental factor. This includes:
Vibration
Vibrations from equipment, such as ventilation systems, near to the weighing system can cause the load cells to misinterpret these vibrations resulting in incorrect weight readings.
This effect can be prevented or reduced by moving the source of the vibration or the scale. Alternatively, you can also use dampening devices such as rubber or cork. There are also specific algorithms that can be used to electronically filter out the vibrations.
Unclean Scales
If a scale isn’t regularly cleaned, this can also cause issues with the accuracy of your scale. Dirt and dust that have built up around (and even inside your scale) can prevent the load cells from completely supporting the load, which will affect the accuracy of your scale.
Wind Loading
Any airflow that can affect your weighing scale is known as wind loading. Any air movement, such as wind or air conditioning units, that can apply pressure on your scale is included in this factor.
A simple way to resolve this is by placing a plexi-glass construct around your scale to protect it from any wind currents. This is often done with balances but is viable for other scales as well.
Air Pressure Differences
If the air pressure is different to the air pressure where the scale was originally calibrated, this pressure differential can lead to inaccurate measurements. To minimise this effect, you can recalibrate the scale in its new location to ensure that it’s correctly pressurised.
4. Interference
Factors that cause interference affect the ability of the scale to display an accurate weight reading.
Moisture
If the scale is not regularly checked, condensation or moisture can build up on the load sensor or cables. This can affect electrical inputs and outputs to become coupled and cause interference in the signals being sent from the load cell to the display indicator.
This can be avoided by using hermetically sealing to prevent moisture from entering.
Temperature
Temperature can also cause interference with signal transmission. If a load cell cable is affected by temperature changes, this can cause wire resistance to increase. As a result, voltage will drop and may cause the display to show something different to the result the output is emitting.
RFI and EMI
Radio frequency interference (RFI) and electromechanical interference (EMI) are both electrical noise sources that can affect weighing accuracy. Examples of RFI and EMI include lightning, two-way radios and large power lines.
This noise affects electrical signals transmitted from your scale, which can result in incorrect weights being displayed.
5. Maintenance
Any scale that is used regularly will result in general wear and tear. By regularly maintaining your scale you can find any issues that may have occurred and prevent them from worsening.
Calibration
At Marsden, we recommend getting your scale calibrated at least once a year. If you use your scale regularly, it may need to be even more often than this. By recalibrating your scale regularly, you’re ensuring that it stays accurate and precise.
Old Parts
As scales get older, general wear and tear will cause scales to become inaccurate. Even with regular maintenance, you may need to replace your scale after a number of years of use. Speak to your service technicians to find their opinion.
Damaged Parts
Although scales can be well protected, there’s always a risk of the inner workings becoming damaged. Malfunction can be caused by water or dust ingress, as well as corrosion.
Damaged Connections
If there is a faulty connection between the load cells and weighing scale, this can cause an incorrect reading to display. This can come about in a number of ways, such poor maintenance or corrosion.
6. User Error
Most of the time the weighing scale is considered the issue, but sometimes user error is the source of the problem. Find 4 examples of human error below:
Cluttered Work Space
This may not seem very important, but a cluttered work space can actually impact the accuracy of a scale. If the scale is propped up on something or if anything touches it, that can cause discrepancies.
Magnets
Magnets can also result in faulty readings as some weighing scales use magnets. Therefore placing other magnets near to the weighing system can skew the readings.
Slope
Weighing scales also require a level surface in order to provide accurate results. If scales are placed on a slope, this can cause inaccurate readings as they expect materials to rest evenly against the load cells. If the scale is sloped this is not possible then this will result in incorrect readings.
Shock Loading
By suddenly dropping a heavy item onto your weighing system, you can create a greater force than the maximum capacity of the scale and damage the weighing system, as well as the load cells.
Related Products
Further Reading
Whether you use medical or industrial scales in your workplace, it’s important to ensure that they’re regularly calibrated. Otherwise you’re opening yourself to a number of risks.
Using a clean analytical balance is one of the first steps to accurate weighing in a laboratory and can actually extend its life cycle. Here’s 5 ways to keep your lab balance clean.
A serviced, accurate weighing scale can help to avoid injuries, accidents and casualties. Find out all of the benefits of regularly servicing your scale here.